Mecmill maximises precision and productivity
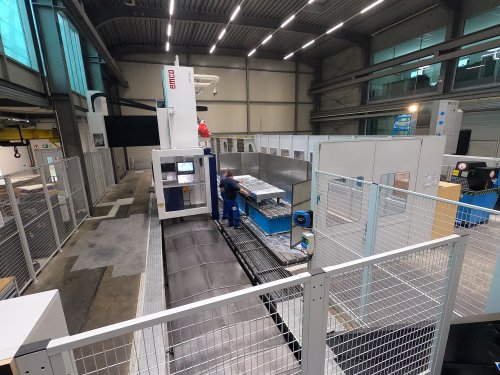
When it comes to manufacturing high-precision moulds in XL dimensions, there are not many companies that can do this to the satisfaction of demanding sectors such as the aviation and automotive industries. Grunewald GmbH&Co. KG in Bocholt can do this and does not compromise on the technology used. The most recent proof of this is the investment in a Mecmill travelling column milling machine from Emco Mecof.
Founded in 1963, Grunewald has developed into a successful medium-sized company with around 200 employees, which is now managed by the third generation of the Grunewald family, brothers Ulrich and Philipp Grunewald. The company’s core competences include the development, design and manufacture of metallic lightweight parts and plastic components – from prototype construction to pre-series and series production. The company also offers innovative tool and mould making, supplying highly demanding sectors such as the automotive and aviation industries.
In toolmaking in particular, in addition to high quality requirements, extreme cost pressure is another factor that makes cost-effective production a real challenge. According to Managing Director Ulrich Grunewald, competitors from Far Eastern countries in particular are entering the market with an aggressive low price policy, which often becomes expensive for customers after a short time. “This is because the quality of these moulds often does not quite meet the requirements, which sometimes necessitates costly reworking,” explains the graduate engineer and business economist, who has also trained as a model maker.
Family business does not compromise on quality
The family business does not get involved in price competitions of this kind. After all, Grunewald doesn’t just think in annual or five-year cycles, but in decades as an owner-managed medium-sized company. In the long term, the only way to score points in this country is with quality products. In order to withstand the high cost pressure, Grunewald makes many other adjustments, which ultimately mean that the moulds and tools manufactured in Bocholt almost always work from the “first shot”.
The basis for this are experienced, highly qualified and motivated employees who are always challenged but also encouraged. With them and a few close partner companies, the company covers the entire value chain, which begins with conception and design and extends through a wide range of manufacturing and production technologies to final quality assurance.
Modern measuring technology is used as well as high-end production technology. Ulrich Grunewald is particularly proud of his latest major acquisition, which was put into operation in 2022 – a new Mecmill travelling column milling machine from Emco Mecof. He explains: “Machines of this size and quality often make the difference. As a partner to the aircraft and automotive industries, we are able to produce even large moulds of up to 14 metres in length for the production of composite components.”
But particularly high tools can also be produced on the Mecmill. Three and a half metres of travel in the vertical axis enable a huge machining range. The machine design even allows significantly higher workpieces to be clamped, as Production Manager Jörg Engler reports: “We recently had to insert complex moulds into an eight-metre-long and five-metre-high component. That was no problem with the Mecmill.”
High flexibility with travelling column machine
When asked why Grunewald ultimately decided in favour of a travelling column machine and not a portal machine, company boss Grunewald immediately cites an important reason: “We have a significantly larger processing area with the same surface area. Or to put it another way, with a portal machine we would need much more space to achieve a similar processing area.” Industrial foreman Engler adds: “The travelling column design also gives us much greater flexibility in terms of machining. A gantry significantly restricts the possibilities, both in terms of height and, for example, angle milling.”
Grunewald and Engler also explain why the Mecmill from Emco Mecof ultimately won the race: “The best overall price/performance ratio weighs just as heavily as the many years of good experience,” says Ulrich Grunewald. Grunewald has had a business relationship with Emco Mecof since the early 1990s. “That was way before my time,” mentions the Managing Director: “And shortly before I joined the company, over 20 years ago, my father bought his first travelling column machine in XL format, the M 5.3, from Emco Mecof. It was built exactly where the Mecmill stands today.”
The M 5.3 always performed its tasks reliably. However, after many years of intensive use, it was no longer up to date. Consumption was too high and some customer requirements in terms of surface quality and accuracy could only be met with long running times. It was therefore necessary to reorientate. For Ulrich Grunewald, the logical consequence was to resume talks with the Italian-Austrian machine manufacturer Emco Mecof.
During the first meetings, it became clear that the existing foundation and even the milling table of the old system could be used for the construction of the new Mecmill. This would significantly reduce the investment required as well as the time needed for installation and commissioning. The figures, data and facts on long-term precision, surface quality, flexibility and productivity of the new milling centre contributed to the decision-making process. Grunewald placed its order in May 2021 and the Mecmill was commissioned at the end of September 2022.
“My only regret is not having bought the Mecmill sooner”
Since then, the correctness of this decision has been confirmed almost daily: “I only regret not having purchased the Mecmill earlier,” reports Ulrich Grunewald, referring to the 30 per cent lower energy consumption, among other things. As Grunewald’s largest milling centre by far always runs in two to three shifts, the savings in this respect add up considerably.
The machine’s high degree of automation also enables numerous unmanned night shifts, as Jörg Engler emphasises: “My employees always try to set up particularly long-running finishing operations at the end of the late shift. Thanks to the automatic tool magazine on the travelling column with 60 positions and the automatic head change with two milling heads, we are able to run almost all programmes overnight or sometimes even over entire weekend shifts.”
Equally helpful for the production manager is the high accuracy and surface quality that can be achieved. For example, customers in the aircraft and automotive industries sometimes require a precision of 7.5 hundredths on curved surfaces of two square metres. The Mecmill achieves this with absolute reliability in five-axis simultaneous milling. At the same time, it achieves consistent surface qualities of Ra = 0.8 µm in fine finishing mode. “We only have to polish if customers don’t allow any milling lines. But even that is much faster now,” says the production manager happily.
Pendulum machining reduces unproductive downtimes
It is not only mega-sized moulds that ensure high utilisation of the Mecmill. If smaller workpieces with a length of a few metres need to be produced, the possibility of pendulum machining pays off. This means that while one side of the machine is being machined, the machine operators set up new components on the other side. This minimises unproductive downtimes.
The new travelling column milling machine is also at its best when it comes to handling and operation. The CNC programmes created on the basis of 3D CAD data are transferred directly to the high-end Heidenhain TNC 640 HSCI control. Clearly displayed, the machine operators perform a final feasibility check and set up the Mecmill. In other words, they equip it with suitable tools, clamp the blank with cranes and set the zero point. Then all that remains is to start the production process and monitor it, especially during heavy roughing.
Productivity is very high for both roughing and finishing. Only with one type of recurring, so-called caul plates (pressure pieces) did the Mecmill initially work more slowly than its predecessor model. Together with Emco service technicians, the Grunewald experts quickly identified the reason for this, as Uwe Urban, Sales Manager Large Machines at Emco, explains: “The vibration alarm on the Mecmill generally sounds a little earlier. Although this is generally useful for protecting the spindle, it had to be readjusted in this case.” Emco’s application engineers have already been at work and have optimised the settings to everyone’s satisfaction. Managing Director Grunewald smiles: “The good thing is that our positive experience with Emco has now been confirmed once again in terms of service friendliness.”
Bildmaterial und Bildunterschriften
Bilder: EMCO GmbH
B01a,b_Emco_Grunewald
Since 2022, Grunewald GmbH has been using a Mecmill travelling column milling machine from Emco Mecof to produce complex moulds in XL format for the aircraft and automotive industries, among other things.
Bilder: EMCO GmbH
B02a,b_Emco_Grunewald
Good cooperation leads to good results. From left to right: Jörg Engler, Production Manager, and Ulrich Grunewald, Managing Director at Grunewald; Uwe Urban, Sales Manager at Emco Mecof, Claas Kuttig, Machine Operator at Grunewald.
Bilder: EMCO GmbH
B03a,b _Emco_Grunewald
Machine operator Claas Kuttig (B03a) finally checks the feasibility of the transferred programme on his clearly laid out high-end control system, while his colleague loads the tool magazine (B03b).
Bilder: EMCO GmbH
B04a,b _Emco_Grunewald
The Mecmill is not only suitable for XL components. Smaller workpieces can be processed in pendulum mode using a partition wall. This means that milling takes place on one side and set-up on the other. This significantly minimises downtimes.
Bilder: EMCO GmbH
B05a,b _Emco_Grunewald
When small cavities need to be produced, the high processing speed of the Mecmill is required.
Bilder: EMCO GmbH
B06a,b _Emco_Grunewald
Unmanned shifts can be realised easily and reliably with the Mecmill from Emco Mecof. Among other things, the fully automatic milling head change contributes to this.
Bild: garten-gg bei pixabay
B07_Emco_Grunewald
Customers from demanding sectors such as the aircraft and automotive industries expect high-precision moulds and tools. Grunewald delivers these one hundred per cent reliably, even in XL format. Thanks in part to high-quality machines such as the Mecmill travelling column milling centre from Emco Mecof.
Bild: DLR
[Foto unterliegt der Creative Commons Lizenz CC_BY-NC-ND 3.0]
B08_Emco_Grunewald
Grunewald produces complex moulds such as this true-to-scale fuselage half-shell for the European Clean Sky 2 aviation project on the Mecmill travelling column milling centre from Emco Mecof.
Bild: Grunewald
B09_Emco_Grunewald
Grunewald manufactures these 7.5 metre long fixtures for the production of landing flaps for the Airbus A320neo with high precision on the Mecmill from Emco Mecof.
About EMCO
EMCO, a mechanical engineering company based in Salzburg, ranks among Europe’s leading machine tool manufacturers. EMCO currently employs about 800 people at a total of 5 production sites in Austria, Germany and Italy. The international, family-run company owes its success to more than 75 years of expertise and experience in the area of machine tool engineering. Today, EMCO stands for top-of-the-line, customised, automated complete solutions for both turning and milling.
To learn more > www.emco-world.com
EMCO GmbH
Salzburger Straße 80, 5400 Hallein-Taxach – AUSTRIA
Biscaro Margot
Phone : +43-6245-891-0
Fax : +43-6245-86965
Margot.Biscaro@emco.at