Natural gait despite amputation – the newly developed D-Ankle prosthesis from Design Pro Technology makes this possible.
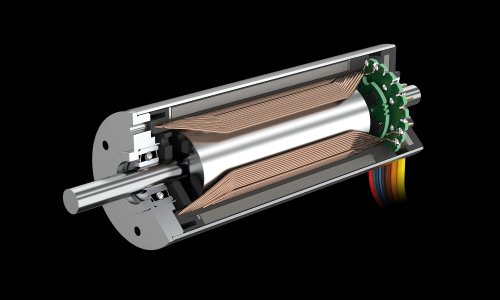
Medical Prosthetic Foot driving with FAULHABER brushless motor
Instead of the usual passive suspension at the foot components, the prosthesis assists its user by means of motor power. As is the case with a natural gait, the artificial foot is actively bent up and down with each step. The gait becomes more harmonious, more stable and less tiring. An intelligent controller finds the correct gait rhythm and a brushless motor from FAULHABER provides the necessary propulsion.
The loss of a leg or part of a lower limb can have many causes. With younger people, the cause is usually a birth defect or an accident. With older people, it is more often cancer, infections and chronic circulatory disorders; the latter is frequently triggered by diabetes. Millions of people are affected worldwide, mostly through the loss of the lower leg. From archeological finds in Egypt and China, we know that attempts to substitute missing body parts with prostheses have been made for at least 3000 years. The stereotypical peg leg from pirate films provides a realistic representation as to what leg prostheses looked like in the past. They were made of wood and leather, were intrinsically stiff and gave their wearers in a limping gait.
From pirate’s peg leg to high-tech orthopedic device
Conventional prostheses can hardly be compared with the modern versions, as these have joints, controlling algorithms and spring-loaded elements made of high-tech materials. With their help, the gait pattern becomes much more natural. Some are even designed for maximum performance: athletes with amputations at the lower leg level who use carbon prostheses achieve outstanding times running over short distances. There have even been serious discussions as to whether the enormous spring force of these carbon-fiber constructs gives amputee athletes an advantage over “normal” runners.
Sport prostheses are designed for fast running, but standing still and performing normal activities while wearing them is difficult, even impossible. Ankle joint prostheses intended for everyday use therefore have a completely different design to the arched “skids” used in competitive sports. Usually mirroring natural anatomy, they consist of a lower leg component and a foot component, connected together by a joint. The passive artificial ankle joint ensures that the prosthesis always remains in a predictable position, however, it allows a very limited range of movement during locomotion.
As the foot recoils – during forward movement – the foot is pressed towards the lower leg; once the foot is kicked out, the elastic force returns the foot to a near perpendicular fixed starting position. “However, this fixed position does not correspond to the natural position of the foot during the transfer phase. There is a risk of the tip of the prosthetic foot getting caught on the ground or on small obstacles,” says Marcin Dziemianowicz. The engineer, whose focus is on biomechanics, founded Design Pro Technology in Białystok (Poland) in 2016 to find innovative solutions for such problems. With an interdisciplinary team consisting of engineers, orthopedic technicians, doctors and designers, the medical technology company develops and manufactures individual orthopedic aids that incorporate the very latest technology.
Active dorsal flexion to reduce the risk of tripping
With its new product D-Ankle, Design Pro Technology has created the first ankle joint prosthesis that actively moves the foot with a motor when walking and holds the foot in an anatomically natural position during the course of each step. Here, so-called dorsal flexion – the bending of the foot toward the tibia – during the swing phase is of crucial importance. “Increasing the distance between the tip of the toe and the ground decreases the risk of tripping,” explains Marcin Dziemianowicz. “With a passive prosthesis, the wearer achieves this by making a circular movement with their hip or by lifting their leg higher. These compensatory movements are unnecessary with D-Ankle; walking becomes more natural and less tiring.”
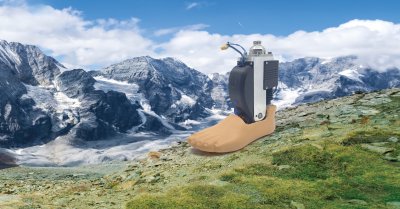
When the prosthetic foot is set down on the ground, its mechanics will perform the natural change in angle during the support phase. D-Ankle is the only prosthesis with active heel-to-toe recoil functionality, including pushing off from the ground for the next step. Here, the motor-driven plantar flexion is activated, i.e. stretching in the joint. It also contributes to a harmonious gait and saves energy. Although the artificial hinge joint is unable to perform the lateral movements that a natural ankle joint allows, they are made possible as passive deformation through the elastic material of the prosthetic foot – carbon fiber. As a result, the foot achieves full sole contact even on uneven surfaces.
The controller detects the gait rhythm
The integrated controller of the prosthesis receives signals from several sensors in order to distinguish between the different phases of a step cycle. A potentiometer measures the angle between the foot and lower leg; a bilateral pressure sensor measures loading at initial contact of the foot as well as unloading in the transfer phase. The accelerometer unit detects the overall movement including speed, foot inclination and path gradient.
“The algorithm merges the signals from few most recent steps and evaluates them,” says Marcin Dziemianowicz, explaining the operating principle. “From this data, it derives the gait rhythm and the optimum foot position for each step phase. For example, the ankle joint is bent more when walking uphill than when walking on a level surface, and also the take-off force is increased to make walking uphill easier. On downward slopes, it’s the other way round so that the best possible contact between sole and ground can be achieved. Furthermore, a smartphone app can be used to adjust parameters such as take-off force, the sensitivity of the pressure sensor or the length of a step cycle phase.”
Sporty drive with great endurance
The integrated drive ensures that the control signals are converted into the appropriate movement. At its heart is a brushless motor of the BP4 series from FAULHABER, the power of which is transferred to a lead screw. Motor and lead screw rotate in both directions and thus achieve active dorsal and plantar flexion of the foot. The high energy efficiency of the drive enables an operating time of 12 hours on one battery charge. The motor also tolerates the considerable heat emission that can occur in everyday operation.
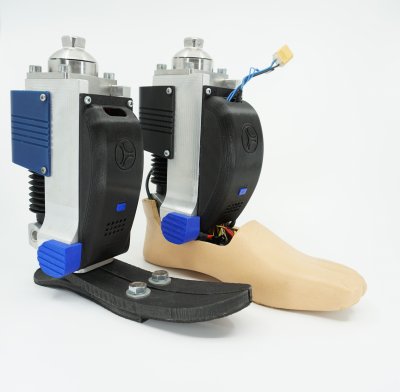
“Our objectives were altogether quite sporty,” recalls Marcin Dziemianowicz. “The motor was to be able to emulate a jogging motion – with three steps per second, or three complete cycles of dorsal and plantar flexion. Furthermore, rapid changes in pace and direction were to be possible. For this application, you need very high speed and high torque in the smallest possible volume and with the lowest possible weight. We tried out various drive solutions from leading motor manufacturers. With FAULHABER, we not only found the most suitable product, but also received outstanding technical support.”
After extensive and successful trials with test amputees, the foot prosthesis will be/was introduced onto the market at the end of 2023. Its standard adapter allows it to be attached to any modular prosthesis stem. Individual prosthesis adjustment is carried out by an orthopedic technician. The height of the heel can be varied so that D-Ankle can also be worn in women’s heeled shoes. Should the battery charge not be enough after a very long day, the wearer can continue to walk as they would with a passive prosthesis.
“With active movement of the foot, we are quite literally making huge steps both toward natural movement anatomy and toward improved support of amputees,” says a pleased Marcin Dziemianowicz. “After the experiences with this product and the great cooperation with FAULHABER, we have a number of ideas on how to utilize the compact motor power for other prostheses.”
Tags: Markets, Products Category, Medical, Prosthetics, Brushless DC-Motors
Company box: The drive experts from Schönaich
FAULHABER is specialized in the development, production and deployment of high-precision miniaturized and miniature drive systems, servo components and drive electronics with up to 200 watts of output power. This includes putting into effect customer-specific packaged solutions as well as an extensive range of standard products, such as Brushless Motors, DC-Micromotors, Encoders and Motion Controllers. The FAULHABER trademark is recognised worldwide as a symbol of high quality and reliability in complex and demanding application areas, such as medical technology, factory automation, precision optics, telecommunications, aviation and aerospace, and robotics. From the powerful DC-motor with a continuous torque of 200 mNm to the filigree micro drive with an outer diameter of 1.9 mm, the FAULHABER standard range can be combined in more than 25 million different ways to create the optimum drive system for a particular application. At the same time, this technological construction kit is the basis for modifications which allow to configure special versions to meet the specific needs of customers.
www.faulhaber.com