Today, every large event includes an elaborate laser show. Laser projections are used at trade fairs, in advertising, art, and at architectural events. The magically glowing light patterns are made possible by highly complex technology, and at many of the most spectacular installations this technology is provided by Berlin-based LaserAnimation Sollinger. When it comes to the alignment of beams and the creation of effects, motors from FAULHABER play an important role in the company’s laser projectors.
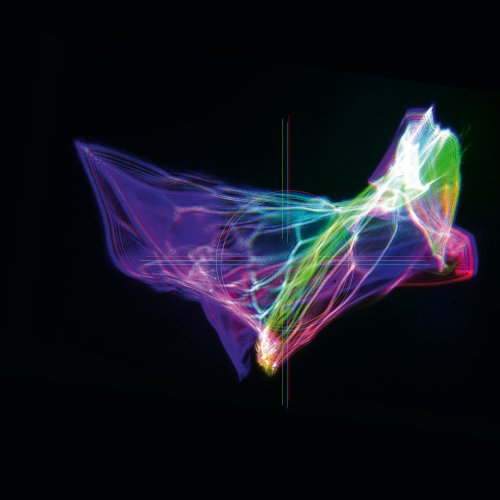
Caution: You may get hooked! Once you click on the project examples on the website of LaserAnimation Sollinger, you may find it difficult to leave again. But the photos and videos on the computer screen are hardly capable of reproducing the actual effect that the laser projections have on site during a performance.
One example is the “Global Rainbow” by the artist Yvette Mattern: seven brightly colored very powerful laser beams shine towards the sky from Berlin’s Ernst-Reuter-Platz in the direction of the Victory Column and change the vibe of an entire city center. Or ‘Another Moon’ by the artist duo Kimchi and Chips, where a second moon appears in the sky over the Zeche Zollverein in Essen. Or the fast-paced show at the closing ceremony of the Winter Olympics in Pyeongchang… these are just a handful of many examples.
Light pen with a diameter of four millimeters
The often surprising and sometimes breathtaking light effects are based on the unique qualities of the laser beam. In terms of intensity, beam focus, and range, it outperforms light beams from other artificial sources many times over. On the other hand, the laser is subject to optical and technical limitations, as sales manager Richard Schäfer explains: “The beam is usually very small. With our devices, its diameter is usually around 4.0 millimeters. So only a small dot appears on a projection surface.”
In order create a pattern – such as a logo, lettering, or cartoon-like moving images – laser projection relies on the inertia of the human eye. To be precise, it is the image processing in the brain, which also creates a continuous progression in a film made up of 24 individual frames per second. If the laser beam moves fast enough, the person “sees” the projected animation instead of a point of light darting around. To achieve this, the beam in the projector is deflected by means of two mirrors – one each for the x and y axes. Its movement is induced electro-magnetically and reaches a very high speed.
Another limitation is the color. The color of a laser depends on the laser-active material in which the beam is generated. In the case of laser projection, it is the semiconductor, since diode lasers or Coherent OPSL sources are used here. But laser diodes can only produce a few basic colors, mainly red, green, and blue. The high-end devices from LaserAnimation Sollinger also have Coherent OPSL sources for yellow, orange, and cyan. To produce a white beam, beams of multiple colors must be “collinearly superimposed.” The same is the case for other colors: in order to create the different tones of the entire palette, the intensity of the individual rays is modulated.
Not even a hundredth of a degree of deviation is allowed
The trick is to superimpose the different laser sources, each with different wavelengths, as collinearly as possible. The more precisely this is carried out, the sharper and more precise the final beam will appear to the human eye. This is where special optical filters, so-called “dichroic filters,” are used, which deflect certain wavelengths while other wavelengths (colors) beam through the glass filtrate. This is how different laser beams can be “superimposed” to form a single beam. So what looks like a “white” ray to the human eye is ultimately the combination of red, green, and blue sources.
But that only works if the beams stay together very precisely and, above all, for a long time and at a great distance, because laser installations often have to be visible from hundreds of meters or even several kilometers away. The dichroic filters have to be adjusted with the appropriate precision, as Richard Schäfer explains: “A deviation of one hundredth of a degree results in an offset of 1.7 centimeters per one hundred meters. This means that the individual colors are no longer on top of each other and can be distinguished by the human eye – the color mixing effect is lost.”
Now, it’s not unheard of that a device from LaserAnimation Sollinger leaves the premises in Berlin to be set up a day later, for example, for a laser show on the Burj Khalifa in Dubai. After minus twenty degrees on the cargo flight, the housing heats up to sixty degrees or more in the desert sun. Despite high-quality materials and sophisticated fastening technology, a certain level of distortion in the optics is inevitable. This means that the position of the dichroic filters may need to be slightly readjusted. This is the reason why the dichroic mirror holders are equipped with a drive: brushless DC motors from FAULHABER with integrated gears are used for software-controlled fine adjustment to at least a thousandth of a degree.
Optical gratings for breathtaking effects
Another motor is used for protection. To prevent the intense laser light from penetrating the human eye in an uncontrolled manner, the projectors are equipped with a two-stage switch-off mechanism. In addition to an electronic protective circuit, there is also a mechanical shutter for emergencies. Its flap is held open during regular operation by a motorized rotary magnet. In the event of a fault, the safety circuit stops the motor and allows the flap to fall into the beam exit.
Other drives from FAULHABER are used in the grating module. Diffraction grating is an optical element that uses the deflection of light rays when passing through very narrow gaps. In addition to beams and graphics, a laser projector can also generate a variety of patterns and effects, such as a kind of artificial polar light or the wafting, abstract forms of Robert Henke’s “Destructive Observation Field”: A light object that changes continuously and looks like a mix between cosmic fog and biological cell structure, reflecting the micro- and macrocosm, as it were. The effects can not only be produced on a projection wall, but also freely suspended in space.
The wheels in the grating module are positioned by stepper motors to select a specific grating for the projection. The circular gratings themselves are set in motion by brushless DC motors, which in turn creates its own optical effect that can range from wild fidgeting to meditatively slow changes in the image at a snail’s pace.
Highest demands on drives
“For these types of effects, we often use several projectors,” explains Richard Schäfer. “They can only unfold their effect if the gratings move completely synchronously, at the highest and lowest speed as well as in start/stop operation with constant changes of direction.” The projectors and the grating modules are full of technology, which means that the installation space is extremely tight. Only very small motors can be accommodated here.
Maximum precision and repeatability are additional minimum requirements. The integrated backlash-free gears play an important role here. When asked about the beginning of the collaboration with FAULHABER, Richard Schäfer replies that it must have been before his time. Looking for the very first order, he finds the year 2003. This means that FAULHABER motors have stood the test of time for this demanding application over the course of twenty years: “We build top of the line devices for laser projections. To do this, we need drives that are on the same level.”
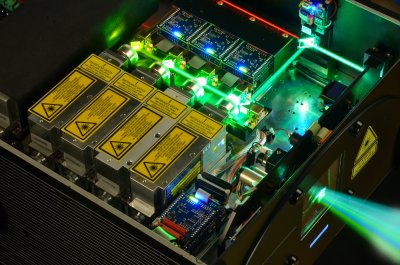
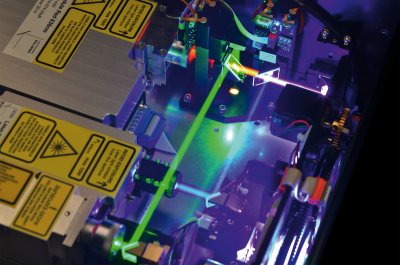
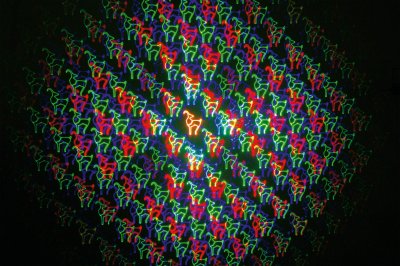
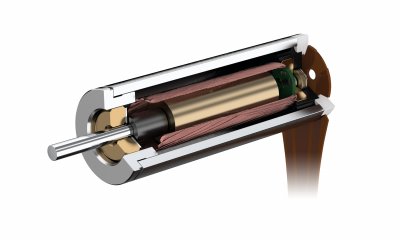
Company box: The drive experts from Schönaich
FAULHABER is specialized in the development, production and deployment of high-precision miniaturized and miniature drive systems, servo components and drive electronics with up to 200 watts of output power. This includes putting into effect customer-specific packaged solutions as well as an extensive range of standard products, such as Brushless Motors, DC-Micromotors, Encoders and Motion Controllers. The FAULHABER trademark is recognised worldwide as a symbol of high quality and reliability in complex and demanding application areas, such as medical technology, factory automation, precision optics, telecommunications, aviation and aerospace, and robotics. From the powerful DC-motor with a continuous torque of 200 mNm to the filigree micro drive with an outer diameter of 1.9 mm, the FAULHABER standard range can be combined in more than 25 million different ways to create the optimum drive system for a particular application. At the same time, this technological construction kit is the basis for modifications which allow to configure special versions to meet the specific needs of customers.
www.faulhaber.com